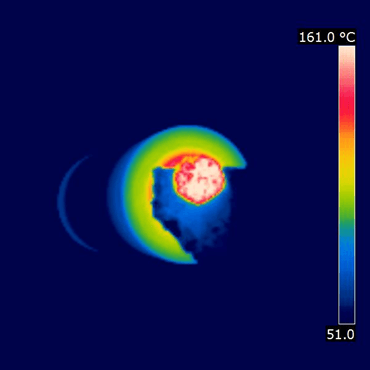
Facility Underground Coal
This case study describes the challenges of mining company Y with underground conveyor reliability and safety.
Challenges
Y’s underground coal mine uses conveyor systems to transport materials to the surface for processing. The company had the following challenges:
Соal mine experienced several fires caused by idler failure in the trunk system Loop Take-Ups.
Inspection personnel were hired to periodically check rollers to increase conveyor reliability. However, rollers regularly failed between inspection intervals and exceeded statutory legal temperature limits.
The Loop Take-Ups were difficult to access and inspect as they were not accessible without isolating the conveyor and removing the guards.
Inspection personnel were hired at a cost of $1,500 per day, two times per week, which equals to $156,000 p/a.
During planned maintenance, Y decided to adopt Smart-Idler® system to avoid employing inspection personnel every 2 weeks and improve conveyor reliability and safety. In doing so, they installed rollers with Smart- Idler® sensors at all LTU locations instead of ordinary rollers. Due to this, Y was able to:
- predict exact roller failures
- only replace damaged rollers
- reduce operational downtime
- reduce yearly costs by over 60%
The cost of adopting the Smart-Idler® system was only $42,840 p/a in hardware and $1,000 p/m in software as opposed to the $156,000 p/a of inspection personnel costs.
Results.
By employing the Smart-Idler® system, Y was able to predict individual roller failure, eliminate the need for inspection personnel, avoid illegal statutory temperature breaches and increase conveyor reliability and personnel safety. All rollers are now monitored 24/7 and leading indicators of failure are reported to maintenance personnel in real time.
Achieved >60% cost savings
Delivered 100% statutory compliance